Brushless Motors BMU Series
BLM5200HPK+5AB10B+BMUD200-A
Product Classification | Product Name | List Price | Shipping Date |
---|---|---|---|
Motor | BLM5200HPK | 216.00 € | Up to 5 pcs Estimated Ship 3weeks |
Gearhead | 5AB10B | 273.00 € | Up to 5 pcs Estimated Ship 4weeks |
Control Circuit | BMUD200-A | Not available for purchase |
Included
- Motor: None
Gearhead: Parallel Key
Control Circuit: CN1 connector, CN4 connector
Specifications
Characteristics
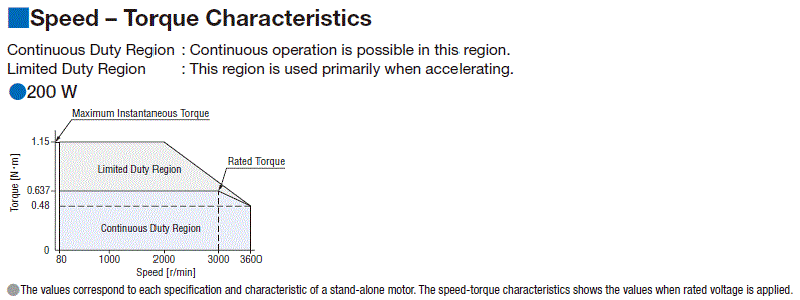
Speed - Torque Characteristics
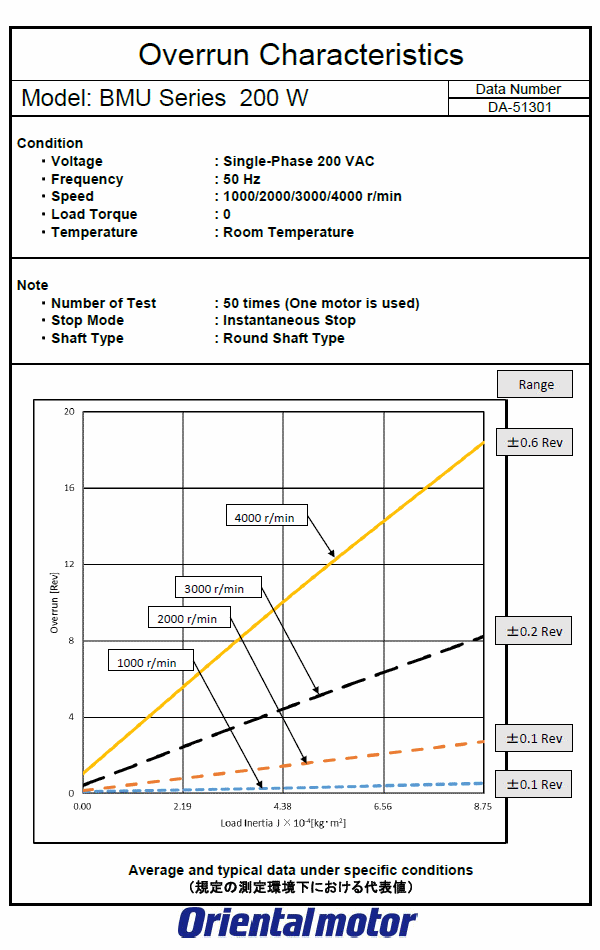
Overrun (Representative Value)
Dimensions

Motor/Gearhead
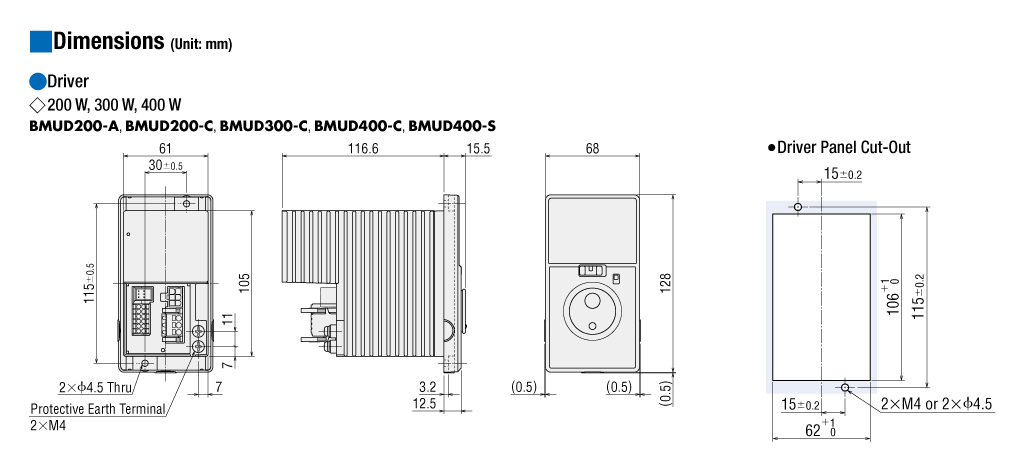
Control Circuit

Connection Cable (When Selected)
Data Download
Other Specifications
Common Specifications
Item | Specifications | |
---|---|---|
30 W, 60 W, 120 W | 200 W, 300 W, 400 W | |
Speed Setting Methods | Digital setting with dial 4 speed settings |
|
Acceleration Time and Deceleration Time |
Analog Setting:
0.1~15.0 seconds: (Time from stop to rated speed)
Common setting for acceleration/deceleration time with acceleration/deceleration time potentiometer* Digital Setting:
0.0~15.0 seconds (set time from current speed to setting speed)
Acceleration time and deceleration time can be set individually for each operation data*
|
|
Input Signals | Photocoupler Input Input Resistance: 5.7 kΩ Operated by Internal Power Supply: 5 VDC Connectable External DC Power Supply: 24 VDC −15∼+20% Current 100 mA min. Sink input/source input Supported through external wiring | Photocoupler Input Input Resistance: 6.6 kΩ Operated by Internal Power Supply: 5 VDC Connectable External DC Power Supply: 24 VDC −15∼+20% Current 100 mA min. Sink input/source input Supported through external wiring |
Arbitrary signal assignment to X0∼X2 input (3 points) is possible. [ ]: Initial setting [FWD], [REV], [M0], M1, ALARM-RESET, EXT-ERROR, H-FREE |
Arbitrary signal assignment to IN0∼IN4 input (5 points) is possible. [ ]: Initial setting [FWD], [REV], [M0], [M1], [ALARM-RESET], EXT-ERROR, H-FREE |
|
Output Signals | Photocoupler and Open-Collector Output External Power Supply: 4.5∼30 VDC 100 mA max. Sink output/source output Supported through external wiring |
Photocoupler and Open-Collector Output External Power Supply: 4.5∼30 VDC 100 mA max. Sink output/source output Supported through external wiring |
Arbitrary signal assignment to Y0, Y1 output (2 points) is possible. [ ]: Initial setting [ALARM-OUT1], [SPEED-OUT], ALARM-OUT2, MOVE, VA, WNG |
Arbitrary signal assignment to OUT0, OUT1 output (2 points) is possible. [ ]: Initial setting [ALARM-OUT1], [SPEED-OUT], ALARM-OUT2, MOVE, VA, WNG |
|
Protective Function | When the following protective functions are activated, ALARM-OUT1 output turns OFF, and the motor will come to a coasting stop. The alarm code will be displayed at the same time. (Instantaneous stop for external stop only) Overcurrent, main circuit overheat, overvoltage, undervoltage, sensor error, overload, over-speed, EEPROM error, initial sensor error, prevention of operation at power-on, external stop |
|
Maximum Extension Distance | 10.5 m between motor and driver [when a connection cable (for relay) is used] | |
Time Rating | Continuous |
Overload Alarm Detection Time
The overload alarm is generated if the operation goes beyond the continuous duty region.
The detection time for this overload alarm can be set from 0.1 to 60.0 seconds arbitrarily. (Initial value: 30.0 seconds)
However, an alarm is generated for a max. length of 5 seconds in the following cases.
- If an applied load goes beyond the limited duty region
- If the output shaft is locked
General Specifications
Item | Motor | Driver | |
---|---|---|---|
Insulation Resistance | 100 MΩ or more when a 500 VDC megger is applied between the windings and the case after continuous operation under normal ambient temperature and humidity. |
After continuous operation at normal ambient temperature and humidity, the measurement value between the power supply terminal and the protective earth terminal and the power supply terminal and the I/O terminal is 100 MΩ min. using a 500 VDC megger. |
|
Dielectric Strength | No abnormality is observed even with an application of 1.5 kVAC at 50 Hz between the coils and the case for 1 minute after continuous operation at normal ambient temperature and humidity. |
After continuous operation at normal ambient temperature and humidity, no abnormality is observed even if 50 Hz, 1.5 kVAC is applied between the power supply terminal and the protective earth terminal, and 50 Hz, 1.5 kVAC is applied between the power supply terminal and the I/O signal terminal for 1 minute. |
|
Temperature Rise | After rated continuous operation at normal ambient temperature and humidity, the temperature rise of the coil measured value by the thermocouple method is max. 50 °C (max. 60 °C for 300 W and 400 W), and the measured value of the temperature rise of the case surface is max. 40°C (max. 50 °C for 300 W and 400 W)*1. |
After continuous operation at normal ambient temperature and humidity, the measurement value of the temperature rise of the heat sink is 50 °C max. using the thermocouple method. |
|
Operating Environment | Ambient Temperature | 0~+40°C (Non-freezing) |
0∼+40°C (Non-freezing) [0~+35 °C*2 (Non-freezing) only when a driver of 300 W or 400 W type is installed with its front side facing upward. The front side of the driver is the side with the display and setting dials.] |
Ambient Humidity | 85 % max. (Non-condensing) | ||
Altitude | Up to 1000 m above sea level | ||
Atmosphere | No corrosive gases or dust Should not be exposed to oil. Cannot be used in a radioactive area, magnetic field, vacuum, or other special environments. | ||
Vibration | Must not be subjected to continuous vibration or excessive shock. Conforms to JIS C 60068-2-6, "Sine-wave vibration Test Method." Frequency Range: 10~55 Hz, Half Amplitude: 0.15 mm, Sweep Direction: 3 directions (X, Y, Z), Number of Sweeps: 20 times |
||
Storage Conditions*3 | Ambient Temperature | -20~+70°C (Non-freezing) JH Gearhead, JB Gearhead, JV Gearhead: -10~+60°C (Non-freezing) |
-25~+70°C (Non-freezing) |
Ambient Humidity | 85 % max. (Non-condensing) | ||
Altitude | Up to 3000 m above sea level JH Gearhead, JB Gearhead, JV Gearhead: Up to 1000 m above sea level |
||
Atmosphere | No corrosive gases or dust Should not be exposed to water or oil. Cannot be used in a radioactive area, magnetic field, vacuum, or other special environments. | ||
Thermal Class | UL/CSA Standards: 105 (A), EN Standards: 120 (E) | − | |
Degree of Protection*4 | Cable Type: IP40 | IP20 | |
Connector Type Dustproof and Waterproof Specifications: IP67 GFV Gearhead, JH Gearhead, JV Gearhead, Round Shaft: IP66 (Excluding mounting surface of the round shaft type.) FR Gearhead: IP65 JB Gearhead: IP44 |
- *1
- Attach round shaft types to a heat sink (Material: aluminum) of one of the following sizes to maintain a motor case surface temperature of 90 °C max.
30 W Type: 115×115 mm, 5 mm thickness, 60 W Type: 135×135 mm, 5 mm thickness, 120 W Type: 165×165 mm, 5 mm thickness,
200 W Type: 200×200 mm, 5 mm thickness, 300 W, 400 W Type: 250×250 mm, 6 mm thickness - *2
- When installing BMU-400-C facing upward, use it at a load factor of 80% or less.
- *3
- The value for storage condition applies to short periods such as the period during transport.
- *4
- The IP indication that shows the watertight and dust-resistant performance are specified under IEC 60529 and IEC 60034-5. The degree of protection of the connector type is when there is connection of the connection cable. The connector part for driver connection is excluded.
Note
- Do not measure insulation resistance or perform a dielectric strength test the motor and driver are connected.
Permissible Radial Load and Permissible Axial Load
Output | Gear Ratio | Permissible Radial Load | Permissible Axial Load N |
||
---|---|---|---|---|---|
10 mm fFrom the End of the Output Shaft N |
20 mm From the End of the Output Shaft N |
||||
200 W 300 W 400 W |
5 | At 80~1500 r/min | 521 | 663 | 39 |
At 3000 r/min | 365 | 464 | 27.3 | ||
At 3600 r/min | 261 | 332 | 19.5 | ||
10 | At 80~1500 r/min | 977 | 1244 | 88 | |
At 3000 r/min | 684 | 871 | 61.6 | ||
At 3600 r/min | 489 | 622 | 44 | ||
20 | At 80~1500 r/min | 1243 | 1582 | 177 | |
At 3000 r/min | 870 | 1107 | 124 | ||
At 3600 r/min | 622 | 791 | 88.5 | ||
30 | At 80~1500 r/min | 1824 | 2280 | 255 | |
At 3000 r/min | 1277 | 1596 | 179 | ||
At 3600 r/min | 912 | 1140 | 128 | ||
50 | At 80~1500 r/min | 2032 | 2540 | 275 | |
At 3000 r/min | 1422 | 1778 | 193 | ||
At 3600 r/min | 1016 | 1270 | 138 | ||
100 | At 80~1500 r/min | 2888 | 3496 | 422 | |
At 3000 r/min | 2022 | 2447 | 295 | ||
At 3600 r/min | 1444 | 1748 | 211 | ||
200 | At 80~1500 r/min | 3483 | 4216 | 461 | |
At 3000 r/min | 2438 | 2951 | 323 | ||
At 3600 r/min | 1742 | 2108 | 231 | ||
300 | At 80~1500 r/min | 4461 | 5174 | 686 | |
At 3000 r/min | 3123 | 3622 | 480 | ||
At 3600 r/min | 2231 | 2587 | 343 | ||
450 | At 80~1500 r/min | 4461 | 5174 | 686 | |
At 3000 r/min | 3123 | 3622 | 480 | ||
At 3600 r/min | 2231 | 2587 | 343 | ||
600 | At 80~1500 r/min | 5245 | 5921 | 824 | |
At 3000 r/min | 3672 | 4145 | 577 | ||
At 3600 r/min | 2623 | 2961 | 412 | ||
1200* | At 80~1500 r/min | 5245 | 5921 | 824 | |
At 3000 r/min | 3672 | 4145 | 577 | ||
At 3600 r/min | 2623 | 2961 | 412 |
- *200W only
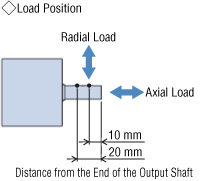
Standards
Regulations and Standards Materials
Documents about compliance with regulations and standards can be downloaded from the "Data Download" tab on the product details page.
(The types of files available for download vary by product.)
Explanations of the Global Laws, Regulations and Standards can be found here.
Information about our compliance with safety standards for each of our product models can be found here.
Hazardous Substances
The product does not contain any substances (10 substances) exceeding the regulation values of the RoHS Directive (2011/65/EU, 2015/863/EU).
For more information about compliance with regulations on chemical substances in Oriental Motor's Products, click here.